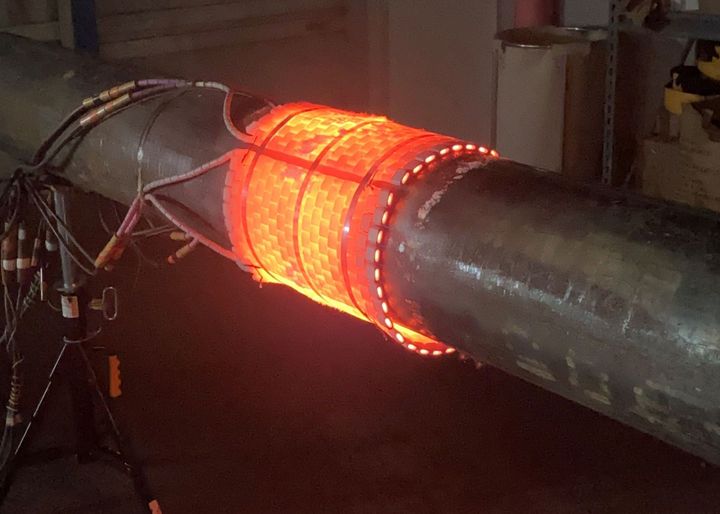
Heat Treatment:
Enhancing Material Properties
Introduction
Heat treatment is a controlled process used to alter the physical and chemical properties of materials, typically metals and alloys. This process involves heating the material to a specific temperature, maintaining that temperature for a set period, and then cooling it in a particular manner. Heat treatment is essential in manufacturing and engineering, enhancing material properties such as hardness, strength, ductility, and resistance to wear.
The Heat Treatment Process
Types of Treatment
Benefits of Heat Treatment
Improved Mechanical Properties
Increases hardness, strength, and toughness, making materials more durable and resistant to wear.
Enhanced Ductility
Softens materials to improve their ability to deform without breaking, which is essential for forming and shaping operations.
Stress Relief
Reduces internal stresses caused by previous manufacturing processes, preventing future distortion or failure.
Grain Structure Refinement
Refines the grain size of the material, leading to better mechanical properties and a more uniform structure.
Increased Resistance to Wear and Corrosion
Enhances the surface properties of materials, making them more resistant to wear and corrosion.
Conclusion
Heat treatment is a vital process in manufacturing and engineering, providing significant enhancements to the properties of materials. By carefully controlling the heating, soaking, and cooling phases, materials can be tailored to meet specific requirements, ensuring they perform effectively in their intended applications. For more information on our heat treatment services and to discuss your specific needs, contact us today!
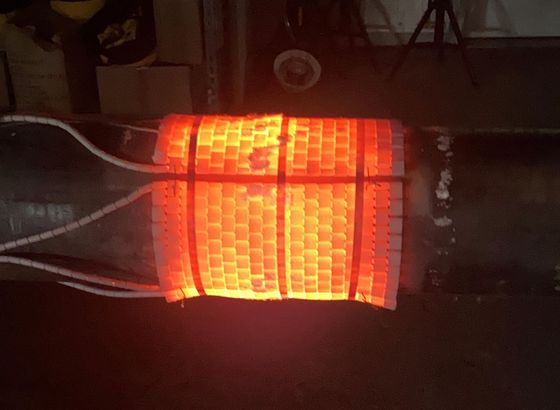